Говоря по-простому, неразрушающий контроль – диагностика объекта с сохранением его целостности и работоспособности. Под объектом может подразумеваться газопровод, буровое оборудование, реакторная установка, резервуар для хранения нефти, грузоподъёмные механизмы… Без таких обследований не обходится ни одно предприятие в нефтехимической, газовой, атомной отрасли и т.д. Везде, где к промышленной безопасности предъявляются жёсткие требования. Виды диагностирования, о которых пойдёт речь ниже, помогают определить надёжность потенциально опасных объектов, оценить их соответствие действующим нормативам и пригодность к дальнейшей эксплуатации.
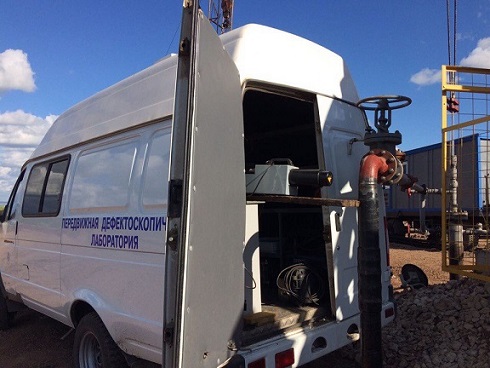
Где проводят неразрушающий контроль?
Примерный перечень зданий, технических устройств, сооружений и их элементов можно найти в ПБ 03-372-00. В нём содержится 10 категорий объектов, на каждом из которых целесообразно проведение НК.
1. Котлы – прежде всего, паровые, водогрейные и электрические. К этой же группе котлонадзора относятся барокамеры, а также сосуды и трубопроводы, рассчитанные на работу под давлением более 0,07 МПа.
2. Наружные и внутренние газопроводы, газовое оборудование, его узлы и детали. Представить себе безопасность систем газоснабжения и газораспределения без проведения неразрушающего контроля – невозможно.
3. Подъёмные сооружения – вышки, грузоподъёмные краны (включая трубоукладчики и манипуляторы), эскалаторы, лифты, канатные дороги и фуникулёры.
4 и 5. Группа объектов, относящихся к горнорудной и угольной промышленности. Речь идёт о зданиях и сооружениях поверхностных комплексов рудников, шахтных подъёмных машинах, главных компрессорных установках и вентиляторах главного проветривания. Скажем честно, не самая распространённая область НК.
6. Оборудование нефтяной и газовой отрасли. Неразрушающий контроль магистральных газопроводов, нефтепроводов и нефтепродуктопроводов – одно из приоритетных направлений. К этой же категории относят буровые вышки, инструмент, агрегаты и пр.
7. Оборудование металлургической промышленности – газопроводы технологических газов, цапфы ковшей, металлоконструкций сооружений, технических устройств и зданий.
8. Оборудование взрывопожароопасных и химических опасных производств. Самая многочисленная группа объектов с точки зрения неразрушающего контроля. Здесь и резервуары, и изотермические хранилища, и печи, и аммиачные холодильные установки, и цистерны, и котлы, и арматура, и технологические трубопроводы, и много чего ещё.
9. Железнодорожный транспорт – подвижной состав, детали вагонов, ж/д пути.
10. Объекты хранения и переработки зерна. В эту категорию включены молотковые дробилки, радиальные и центробежные вентиляторы, воздушные турбокомпрессоры и пр.
Разумеется, список не исчерпывающий. Есть ещё судостроение, авиа- и ракетостроение, атомная энергетика, машиностроение и многое другое.
Основные группы методов неразрушающего контроля
Их классификация изложена в ГОСТ Р 56542-2015. В зависимости от физической «природы» методов дефектоскопии выделяют следующие их виды.
Магнитный контроль
Самая популярная его разновидность – магнитопорошковый метод (МПД). На исследуемую поверхность наносят специальный порошок либо суспензию в виде мелкодисперсной взвеси магнитных частиц в жидкости. После этого при помощи ручного электромагнита или дефектоскопа создаётся магнитное поле. Магнитные частицы оседают вблизи несплошностей. Полученный индикаторный рисунок подлежит рассмотрению и расшифровке – либо невооружённым глазом, либо при помощи УФ-светильников. После этого изделие размагничивают. Магнитопорошковый метод неразрушающего контроля применяется для изделий из ферромагнитных материалов и эффективен для поверхностных и приповерхностных дефектов (до 2–3 мм):
- усталостных трещин,
- волосовин,
- неметаллических включений,
- флокенов,
- несплавлений и прочих несплошностей.
«Слабость» МПД в том, что определить глубину раскрытия обнаруженных трещин с ним не так-то просто.
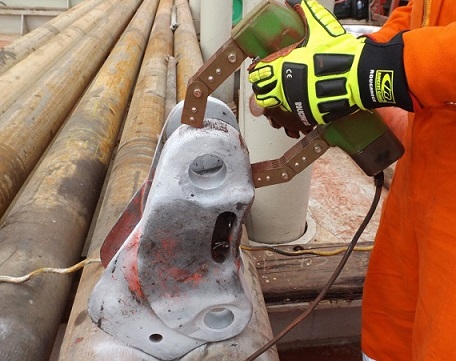
Вихретоковый контроль
Сокращённое обозначение этого метода неразрушающего контроля – ВК. При помощи дефектоскопа с одной или несколькими индуктивными катушками и преобразователей создаётся электромагнитное поле, возбуждающее вихревые токи в исследуемом объекте. Они, в свою очередь, обладают своим электромагнитным полем, которое воздействует на катушки, изменяя электродвижущую силу и сопротивление. Регистрация этих параметров позволяет:
- обнаруживать даже микроскопические дефекты,
- измерять толщину тонкостенного трубного и листового проката,
- оценивать качество термообработки,
- определять глубину поверхностных трещин и пр.
Вихретоковый метод может применяться лишь для неразрушающего контроля токопроводящих материалов и подходит для выявления дефектов на малой глубине. Зато – все измерения выполняются бесконтактным способом, легко поддаются автоматизации и не занимают много времени.
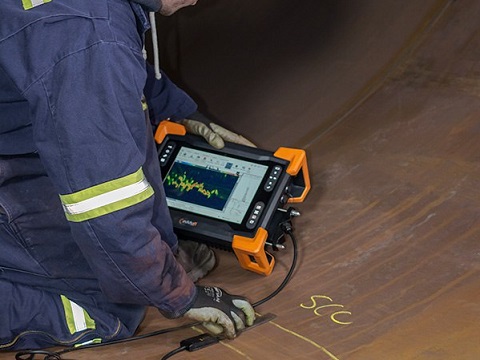
Капиллярный контроль
Считается одним из самых эффективных, простых и доступных методов для обнаружения дефектов, сквозных и поверхностных. Технология предполагает применение специальных индикаторных жидкостей – пенетранта и проявителя. Перед проведением и по завершении осмотра индикаторного рисунка поверхность обрабатывают очистителем. Такой метод неразрушающего контроля ещё называют цветным (ЦД, ПВК). Заполненные пенетрантом несплошности, трещины, складки, несплавления окрашиваются в характерный цвет (чаще всего, красный). На белом фоне остальной поверхности они резко контрастируют, что и позволяет выявлять мельчайшие дефекты. Наиболее существенный недостаток метода – токсичность, повышенные требования к вентиляции в рабочей зоне и средствам индивидуальной защиты дефектоскописта.
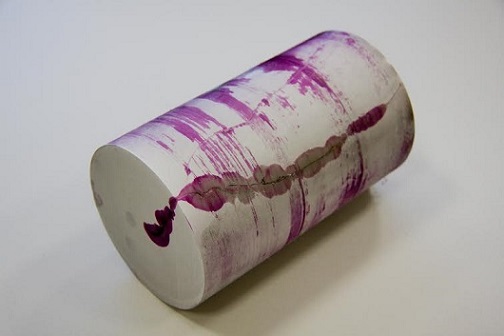
Ультразвуковой контроль
Ультразвуковая дефектоскопия, или УЗК (УЗД) – пожалуй, самый универсальный метод, строго обязательный на самых разных опасных производственных объектах. Применяется практически всюду, начиная диагностикой железнодорожных путей и заканчивая литейным производством. Если в двух словах, то этот вид неразрушающего контроля основан на излучении и/или приёме акустических колебаний и волн в материале. Это могут быть стальные, алюминиевые, чугунные сплавы, а также композиты, полимеры, пластики, стекло, фарфор и пр. Ультразвуковая дефектоскопия хороша тем, что:
- позволяет обнаруживать наиболее критичные дефекты;
- абсолютно безопасна для оператора – в отличие от капиллярного или радиационного контроля;
- подходит как для металлических, так и для неметаллических материалов;
- отлично «вписывается» на производственных предприятиях и полевых объектах, где предъявляются высокие требования к производительности;
- обеспечивает наглядность контроля (у новейших дефектоскопов есть функции построения В-, С-сканов, профилей дна изделия и пр.).
УЗК как вид неразрушающего контроля объединяет множество направлений – традиционный контроль теневым, зеркальным, эхо-методом, TOFD, фазированные решётки, ультразвуковую толщинометрию, акустическую эмиссию, импедансный контроль и т.д. Однако ультразвуковая дефектоскопия не совершенна, поскольку:
- требовательна к качеству поверхности, её шероховатости (нужно предварительно зачищать, удалять окалину, ржавчину, загрязнения, остатки ЛКМ);
- не очень эффективна для обследования металлов с крупнозернистой структурой;
- предъявляет высокие требования к техническим средствам и квалификации оператора – для точной классификации дефектов и оценки их фактических размеров.
С технической точки зрения методы неразрушающего контроля не стоят на месте. Направление УЗК развивается особенно бурно. Топовые российские и зарубежные производители делают всё для того, чтобы упростить работу операторов, повысить информативность и производительность акустической дефектоскопии.